Our Portfolio
Des Plaines River WRF Upgrade & Regional Biosolids Drying
Lake County, Illinois

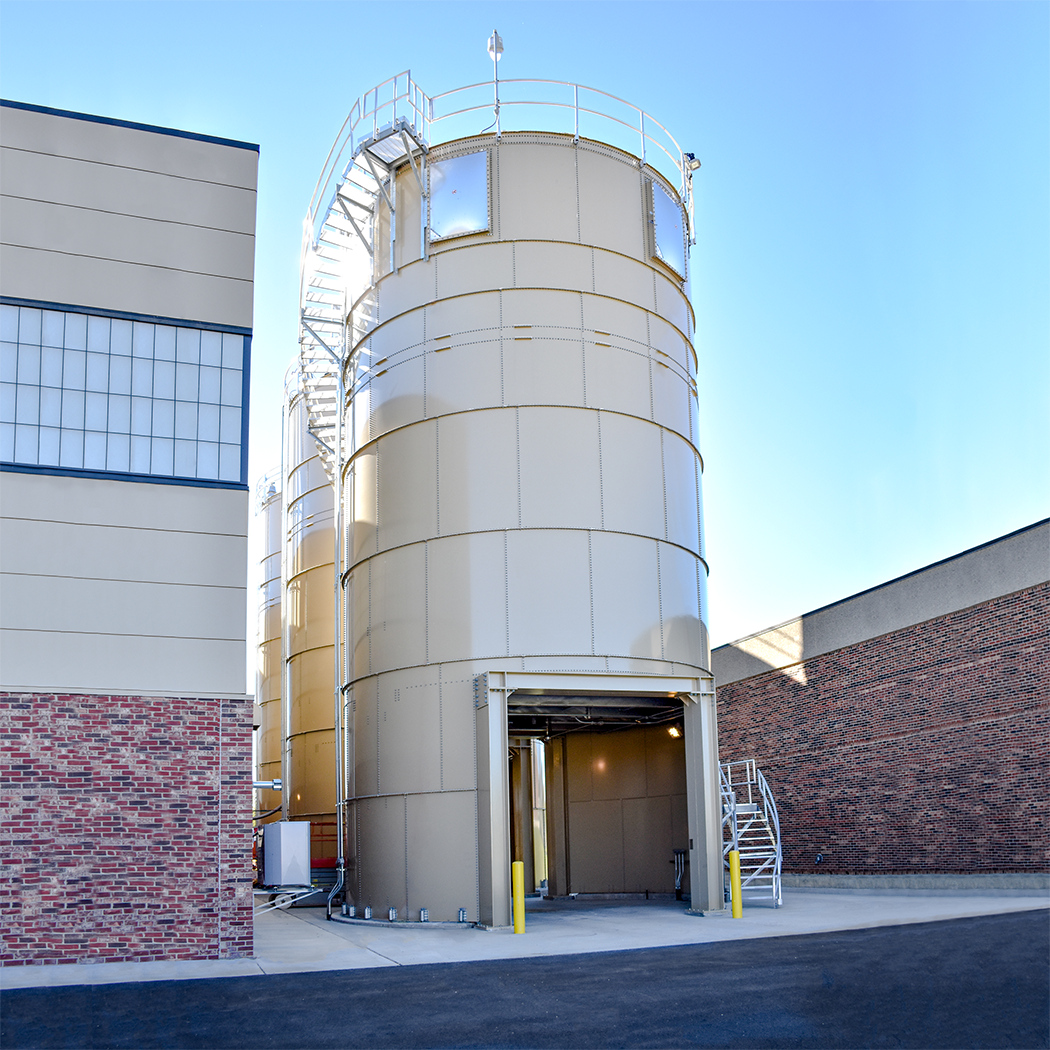
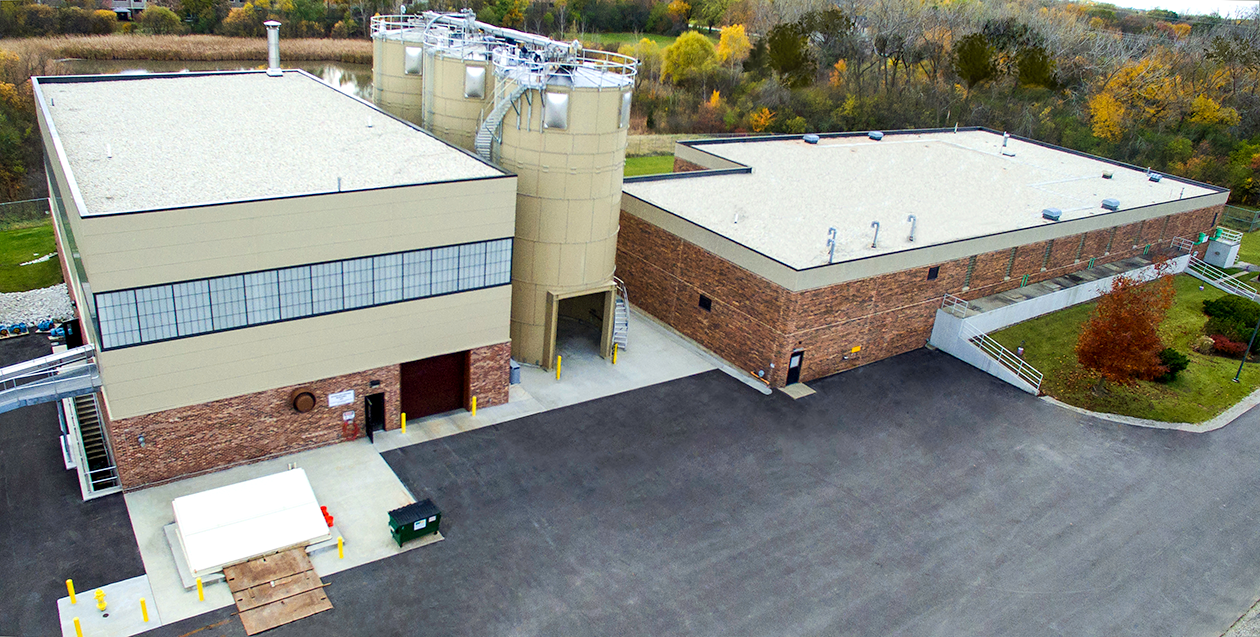
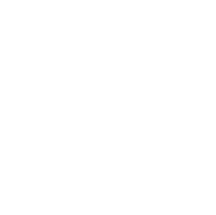
- type:
- Waste Management
- services:
- Facilities planning, Design, Construction administration and inspection
Project Location: Lake County, Illinois
Design Capacity: 16 mgd
Construction Cost: $32 million
The Lake County Public Works Department (LCPWD) owns and operates the 16.0 mgd Des Plaines River Water Reclamation Facility (WRF). LCPWD retained ATI to undertake a Facilities Plan to address regulatory restrictions on effluent phosphorus and biosolids storage. The Facilities Plan identified a regional biosolids drying facility as the least costly alternative on a capital and present worth basis and was the most desirable on a non-economic basis. In addition, to meet the future phosphorus limits, the Facilities Plan recommended modifying the existing aeration basins to incorporate biological nutrient removal (BNR) into the treatment process.
ATI designed a new regional biosolids dryer facility to process the waste sludge from Lake County’s three WRFs. Detailed preliminary design activities included present worth comparison of five different dryer arrangements, tours of full-scale dryer facilities for LCPWD operations personnel, and onsite pilot testing of the selected dryer technology. The new biosolids drying facility features a paddle dryer with capacity to process 140 tons/day of wet cake solids from the three WRFs. The dryer facility produces 23 tons/day of dried product, with solids content exceeding 92% and meeting USEPA 503 regulations for a Class A product. The biosolids dryer facility is fully equipped with the required safety features to conform to industry standards for dust and gas emissions. The dried product is stored in silos adjacent to the dryer building, prior to being loaded in trucks for transport offsite.
The existing aeration basins were modified to incorporate BNR into the treatment process. In addition, to meet the future phosphorus limits, the existing activated sludge facilities were modified for multiple BNR process schemes. The fine bubble membrane diffuser grids were replaced with a new tapered arrangement that included the installation of about 4,000 diffusers. Baffle walls, zone mixers, and recirculation piping were added for the BNR process requirements.
Features
Regional Class A biosolids drying facility
Multiple enclosed screw conveyors for biosolids products
Nitrification and denitrification
Disk filtration for enhanced phosphorus removal
Aluminum sulfate phosphorus polishing system
Disk filter retrofit into effluent filter building
Expansion of the 480V power distribution system for a new biosolids drying building
Switchboard and MCC modifications
In-line and sidestream fermentation to produce VFAs
Building renovations
New 1500kW standby diesel generator system
Grit system improvements